Unraveling the Mystery of Fiber Laser Wobble Welding Focus Height
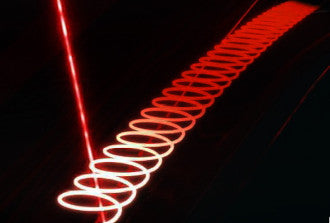
Understanding Fiber Laser Wobble Welding:
Before we delve into the specifics of focus height, let's briefly recap what fiber laser wobble welding entails. Unlike traditional welding methods, which rely on a fixed laser beam, wobble welding introduces controlled oscillations to the laser beam's path. This dynamic movement creates a wider weld seam, enhancing penetration and heat distribution while minimizing defects.
The focus height in laser welding refers to the distance between the laser beam's focal point and the workpiece's surface. This seemingly minor detail holds immense importance as it directly influences the weld bead geometry, heat input, and ultimately, the integrity of the weld joint. Maintaining the correct focus height ensures precise energy delivery, preventing issues such as under- or over-penetration, spattering, and inconsistent weld seam quality.
Equally crucial is the focal point, which marks the spot where the laser beam achieves its maximum intensity. Properly aligning the focal point with the weld seam is imperative for achieving deep penetration, uniform heat distribution, and minimal distortion. Moreover, the focal point's alignment directly impacts the weld's width and depth, crucial parameters that determine the weld's mechanical properties and overall performance.
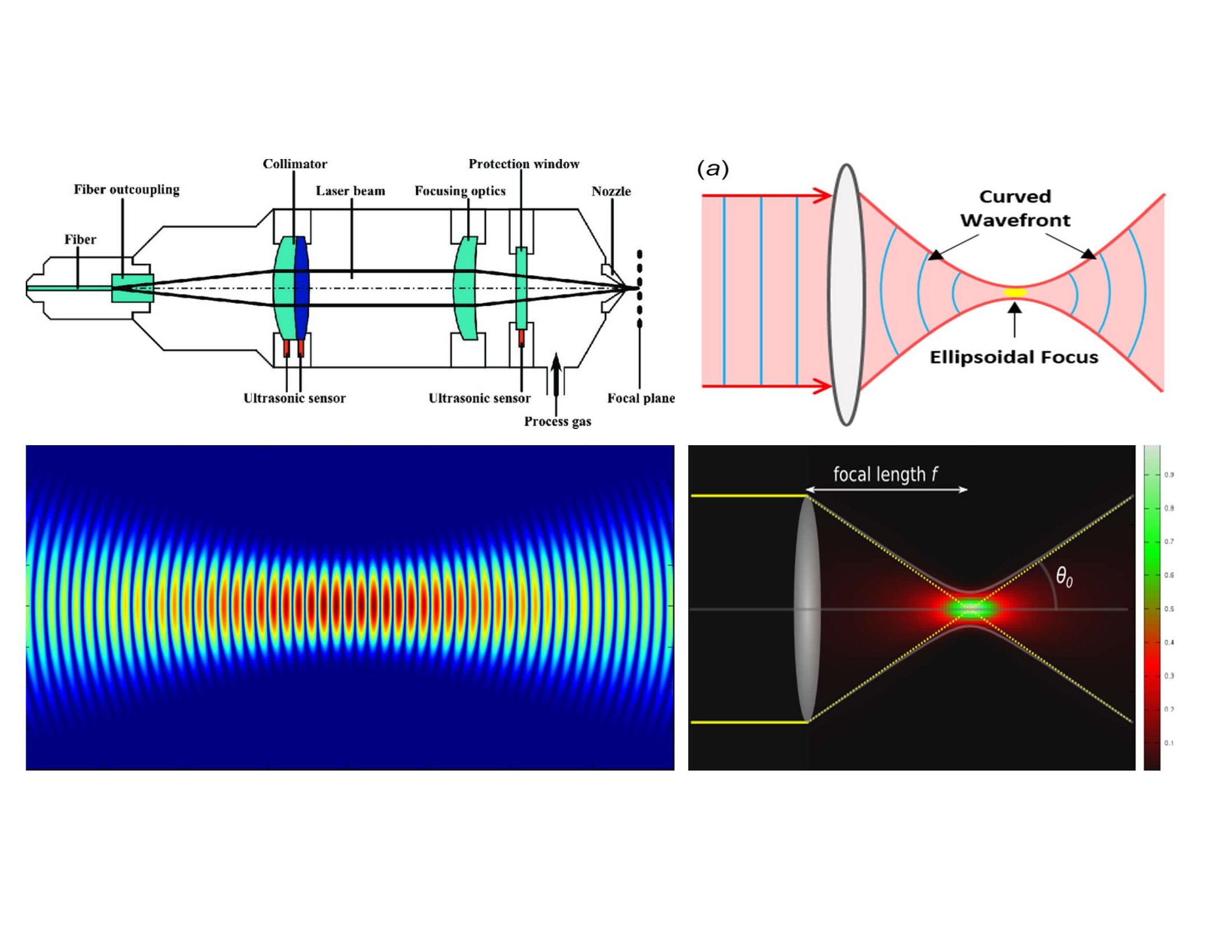
The Role of Focus Height:
Now, let's zoom in on focus height – a critical parameter in fiber laser wobble welding. Focus height refers to the distance between the laser focal point and the workpiece surface. Achieving the optimal focus height is paramount for ensuring consistent weld quality and performance.
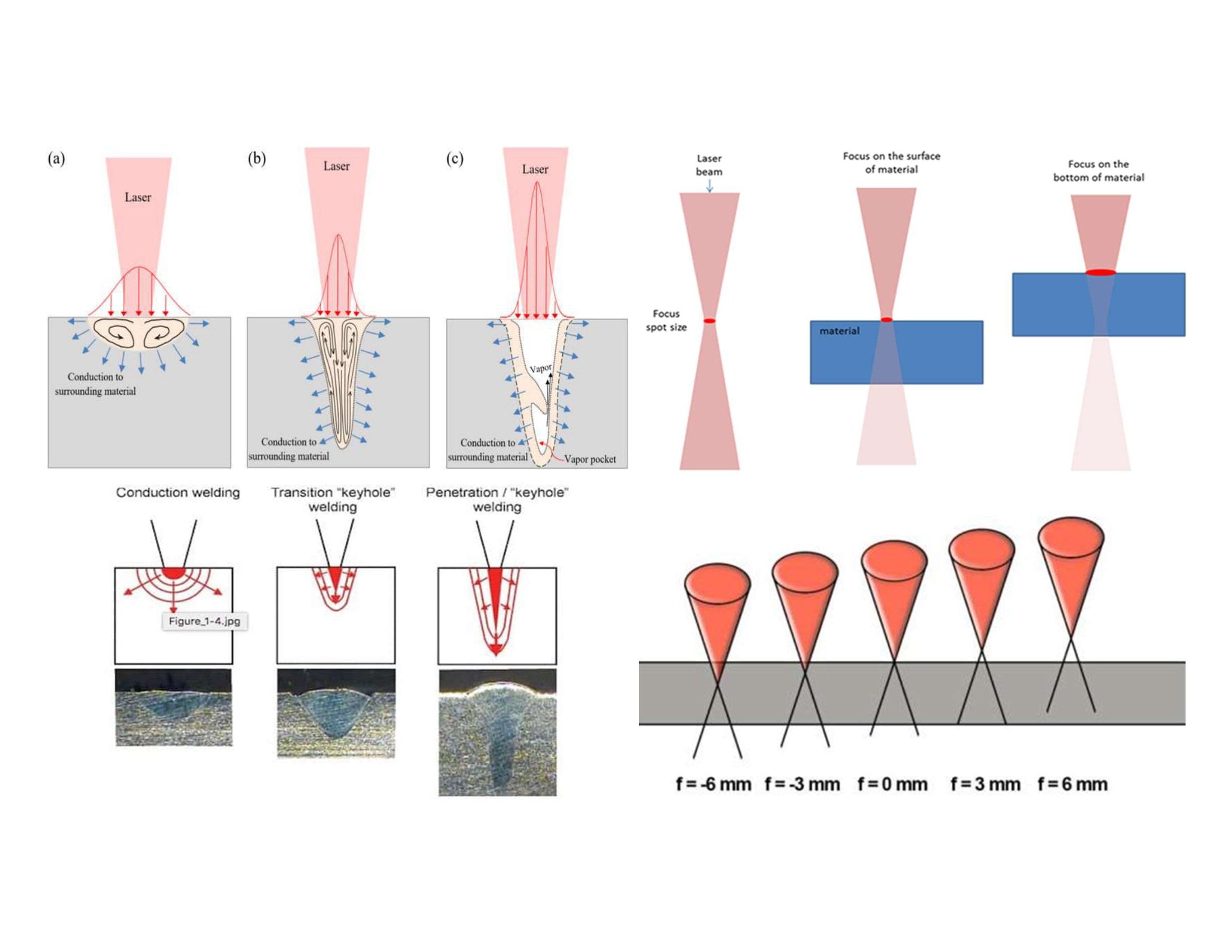
Factors Influencing Focus Height:
Several factors influence the selection of focus height in fiber laser wobble welding:
• Material Thickness: Thicker materials typically require a greater focus height to ensure proper penetration.
• Beam Quality: The quality of the laser beam affects its ability to maintain focus over varying distances.
• Weld Speed: Higher welding speeds may necessitate adjustments to focus height to maintain weld integrity.
• Surface Condition: Surface irregularities or contaminants can affect focus height and weld quality.
• Beam Diameter: The diameter of the laser beam influences the depth of focus, impacting the optimal focus height selection.
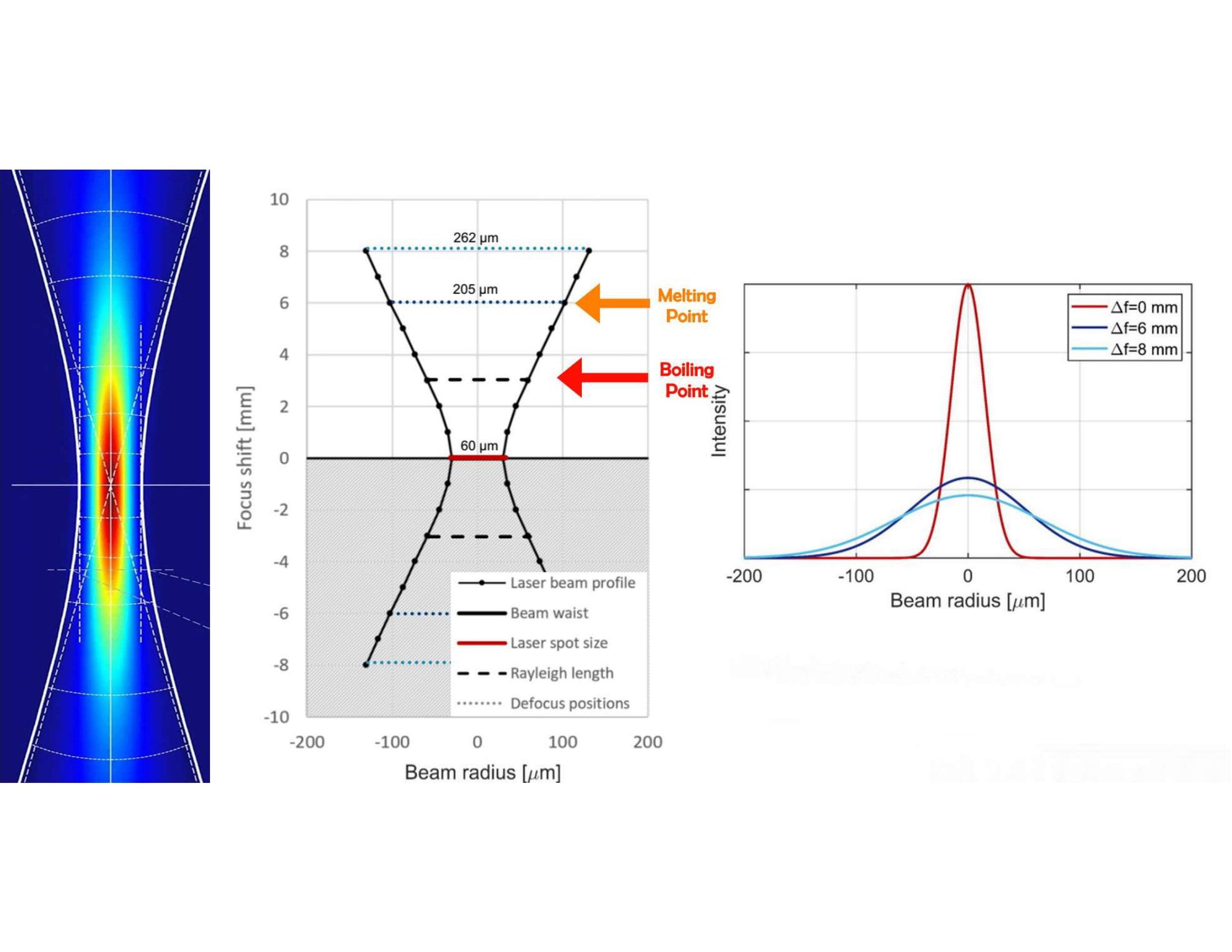
Optimizing Focus Height for Superior Results:
Now, let's explore some strategies for optimizing focus height in fiber laser wobble welding:
• Experimentation and Testing: Conducting test welds across a range of focus heights allows welders to identify the optimal setting for specific materials and configurations.
• Real-Time Monitoring: Implementing monitoring systems that provide feedback on weld quality can help adjust focus height during the welding process.
• Adaptive Control Systems: Utilizing advanced control systems that automatically adjust focus height based on real-time feedback enhances process stability and consistency.
• Operator Training: Providing comprehensive training to operators ensures they understand the importance of focus height and how to make adjustments effectively.
• Collaborative Research: Collaborating with laser manufacturers and research institutions can yield insights into novel techniques for optimizing focus height and improving overall welding performance.
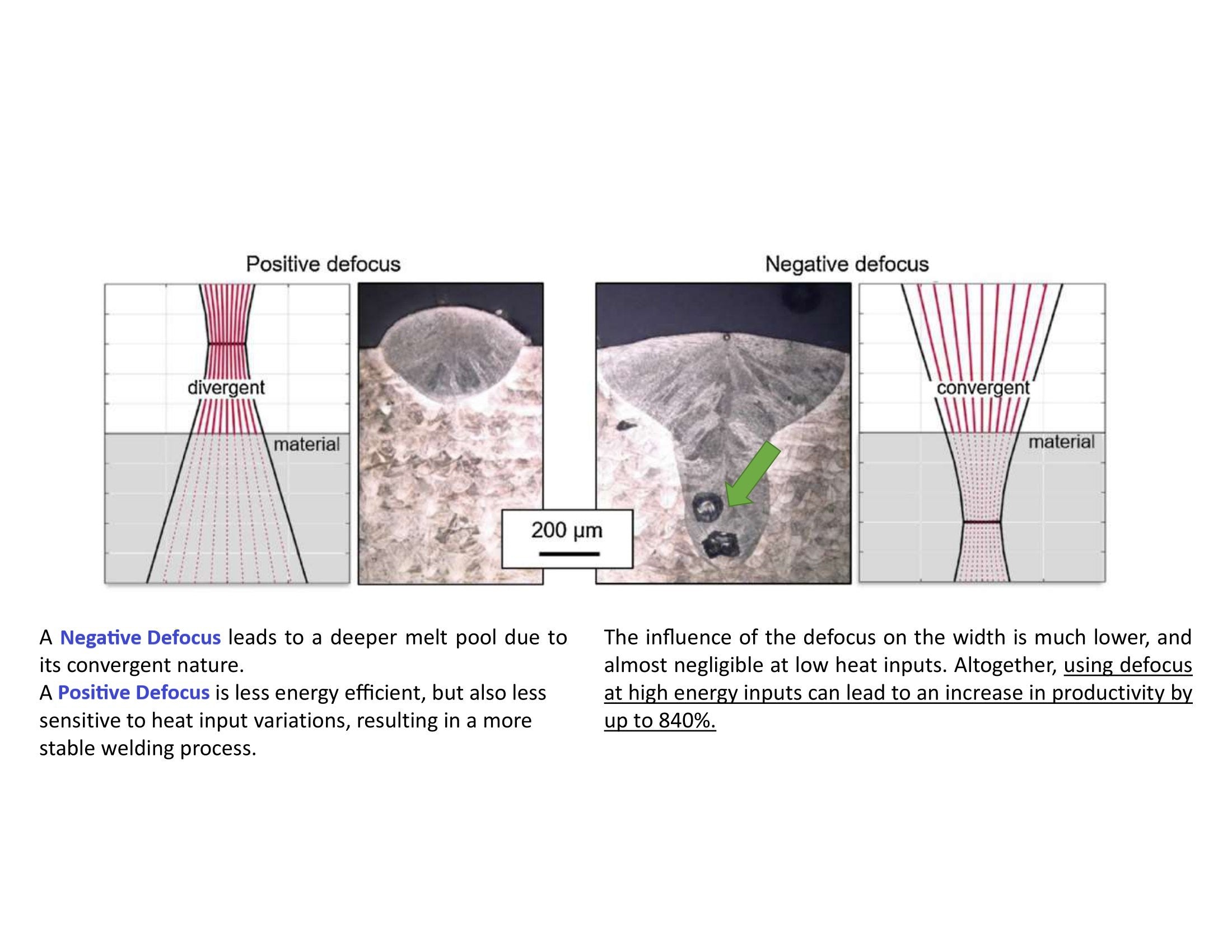
Mastering focus height in fiber laser wobble welding is key to unlocking its full potential. By understanding the factors influencing focus height and implementing effective optimization strategies, welders can achieve superior weld quality, increased productivity, and enhanced process reliability. So, let's continue to explore, innovate, and push the boundaries of welding technology together.
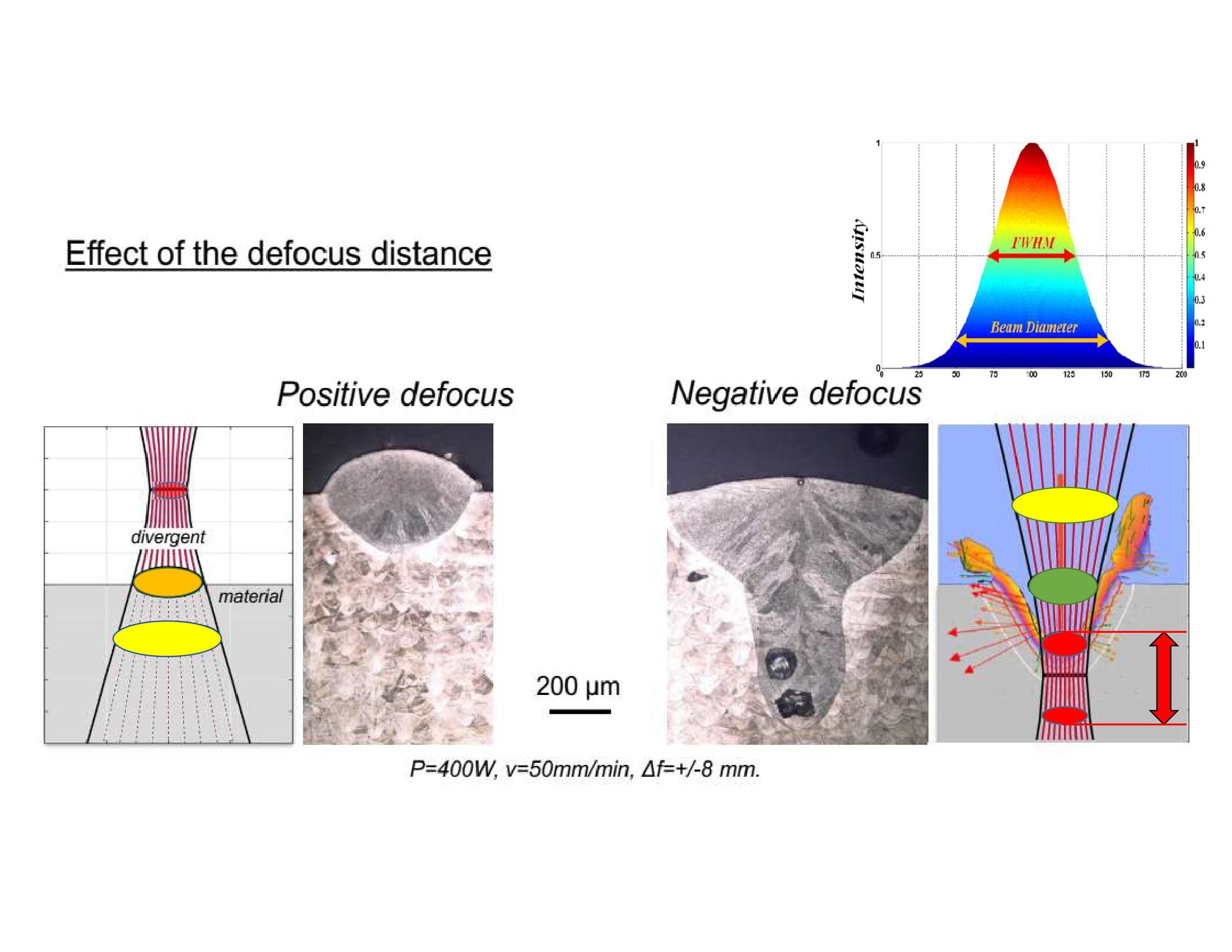